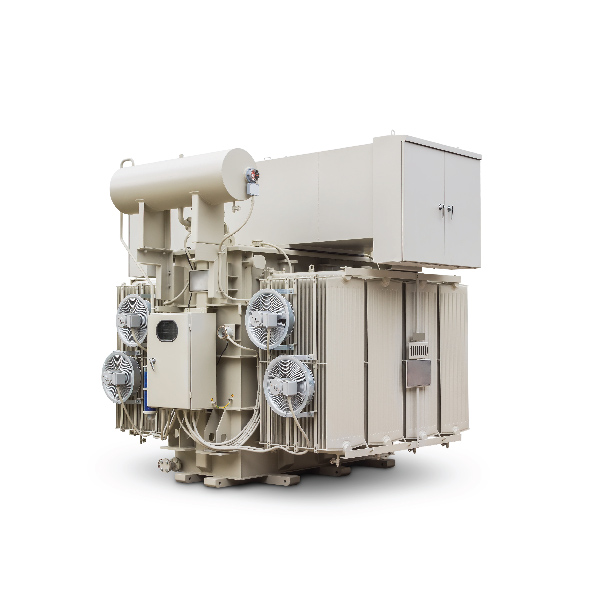
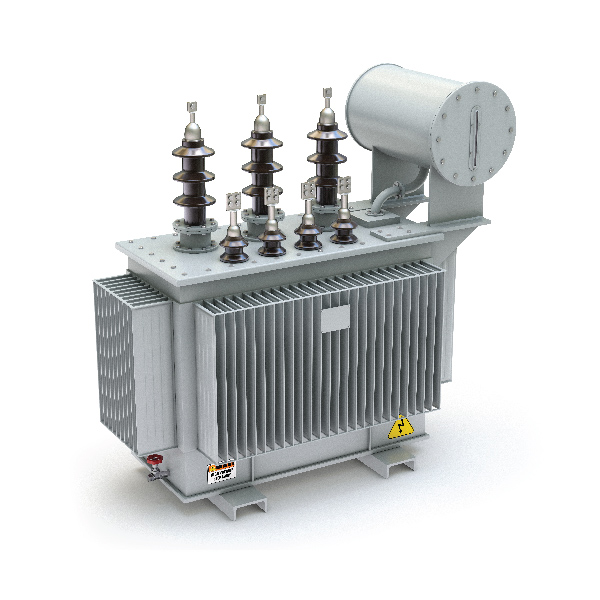
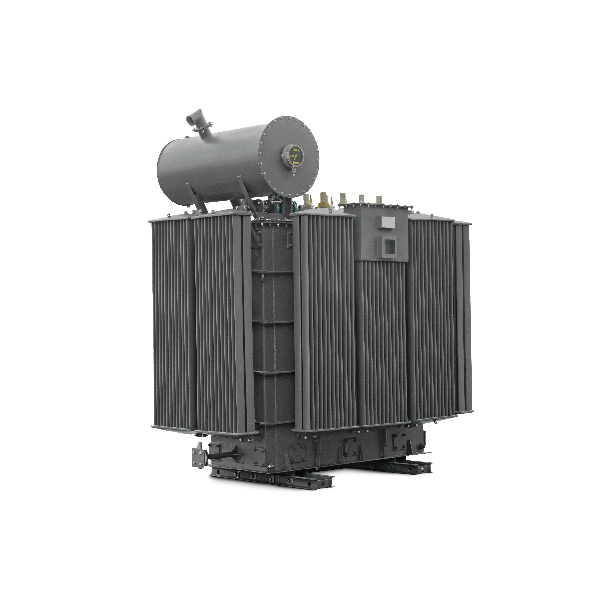
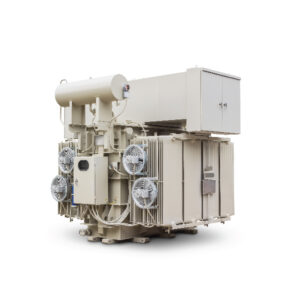
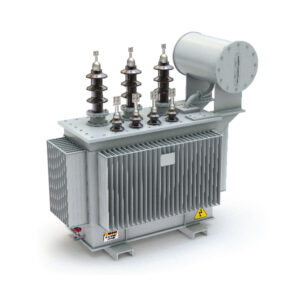
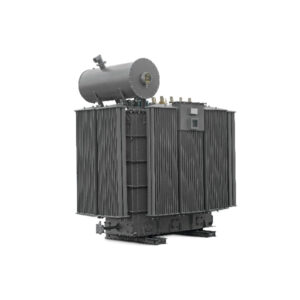
Distribution Transformer
A distribution transformer is a crucial component in electrical systems, providing the final voltage transformation by stepping voltages down within a distribution circuit or from a distribution circuit to an end user or application. These transformers play a vital role in improving safety and efficiency in power systems by regulating voltage levels as needed.
The key components of a distribution transformer include:
- Core and Windings: The core consists of laminated steel sheets to minimize magnetic losses. The windings (primary and secondary) are made of copper or aluminum conductors.
- Oil Tank: The oil tank houses the core and windings and is filled with insulating mineral oil.
- Conservator: Positioned above the oil tank, it maintains oil levels and allows for expansion and contraction during loading.
- Breather Unit: Contains silica gel to absorb moisture in the oil.
- Temperature Detector: Monitors oil temperature and disconnects the transformer if it exceeds safe limits.
- Pressure Relief Device: Prevents excessive pressure buildup.
- Radiator: Helps dissipate heat.
- Bushing: Provides electrical insulation for connections.
Applications:
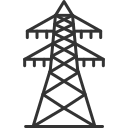
Urban Areas
To supply electricity to homes, offices, and businesses.
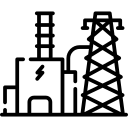
Substations
For isolating equipment during maintenance.
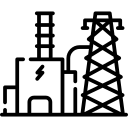
Voltage Conversion
Transforming high-voltage transmission lines to usable voltages for consumers.
Types of Core Materials:
- Cold-rolled, grain-oriented silicon steel (CRGOS): is often thinly laminated to create transformer cores. Due to its high permeability, CRGOS lowers core losses and magnetizing currents, ensuring effective magnetic coupling between windings, facilitating easier transfer of electrical energy from the primary side to the secondary side. Benefits: CRGOS’s crystalline structure and magnetic qualities reduce hysteresis and eddy current losses.
- Laminated Cores: Consist of thin sheets of ferrous metal (usually silicon steel) stacked together. These laminations reduce overheating and circulating currents in the core, resulting in lower energy losses. Removing air gaps between laminations further improves efficiency.
- Amorphous Metal Core: The typical material used for amorphous cores is an alloy called Metglas, composed of iron combined with boron, silicon, and phosphorus. It is formed into thin foils (approximately 25 μm thick) that rapidly cool from a molten state.
Properties:
- High Magnetic Susceptibility: Amorphous alloys exhibit high magnetic susceptibility.
- Low Coercivity: They have very low coercivity, reducing hysteresis losses.
- High Electrical Resistance: Thin foils lead to low losses due to eddy currents under alternating magnetic fields.
- Comparison: However, amorphous alloys may have lower saturation induction and higher magnetostriction compared to conventional crystalline iron-silicon electrical steel.
Advantages and Applications:
- Efficiency: AMTs significantly reduce core losses (no-load losses) compared to traditional crystalline materials.
- Grid Distribution Transformers: AMTs are commonly used in grid distribution transformers rated around 50–1000 kVA.
- Electric Trains: Amorphous iron is also used in specialized electric motors operating at high frequencies (e.g., 350 Hz or more).
- Advantage: More efficient transformers lead to a reduction in generation requirements and, when using electricity from fossil fuels, result in lower CO2 emissions.
Related Products
Distribution Box
A distribution box is an essential component in electrical systems, serving as the central point for distributing electricity...
Read More
Expulsion Drop-Out Fuse
When the current operating through an electrical circuit exceeds a certain limit, a drop-out fuse trips the...
Read More
Link Drop-Out Fuse
When the current operating through an electrical circuit exceeds a certain limit, a drop-out fuse trips the circuit. This threshold...
Read More
Polymeric Drop-Out Fuse
When the current operating through an electrical circuit exceeds a certain limit, a drop-out fuse trips the circuit. This threshold...
Read More
Our Blog